Sistemas de refrigeração é o nosso assunto da aula de hoje.
Para ver mais conteúdos como esse, acesse nossos Cursos Certificados Vaportec.
Nós vamos falar hoje sobre normas e boas práticas.
Além disso, os procedimentos para trabalho.
Tudo isso em manutenção em sistemas de refrigeração industrial por amônia.
Sistemas de refrigeração: códigos e normas aplicáveis
As boas práticas e cuidados desenvolvidos para usar nos sistemas existentes.
Ainda mais em sistemas de refrigeração por amônia no Brasil.
Baseiam-se então na documentação internacional disponível.
Existe uma comissão de estudos de refrigeração industrial: a CE-55:001.04, da ABNT.
Ela desenvolveu assim uma norma brasileira sobre segurança em sistemas de refrigeração.
É conhecida então como NBR 16069.
A norma está baseada no ANSI/ASHRAE Standard 15-2007.
E usa então as demais normas internacionais. Como referência então para discussão.
A seguir então, os principais documentos disponíveis.
Relacionados à aplicação de Amônia em sistemas de refrigeração.
Normas Brasileiras aplicáveis em sistemas de refrigeração industrial por amônia
• NR-13 – 2008 – Caldeiras e Vasos de Pressão.
Normas Regulamentadoras da Legislação de Segurança e Saúde no Trabalho.
Ministério do Trabalho – Lei nr. 6514 – 22/12/1977.
• P4.261 – Manual de Orientação para a Elaboração de Estudos de Análise de Riscos – CETESB.
Companhia de Tecnologia de Saneamento Ambiental – 13/08/2003.
• NBR 13598 – Vasos de Pressão para Refrigeração.
ABNT – Associação Brasileira de Normas Técnicas – 04/1996
Responsabilidades do operador do sistema
Como iniciar então a operação de um sistema de refrigeração por amônia?
É necessário um conhecimento pleno dos fundamentos básicos de refrigeração.
Incluindo assim as características do ciclo de compressão à vapor.
Além disso, as relações pressão x temperatura do fluido refrigerante.
Bem como as funções e características principais.
Dos componentes dos sistemas de refrigeração. E os aspectos envolvendo a sua segurança.
Não significa que o operador saiba então como projetar um sistema.
Mas, precisa ter conhecimento suficiente dos vários aspectos do mesmo.
Ainda mais sobre o sistema no qual ele opera.
Sua função então é operar o sistema de maneira segura.
Conforme os requisitos de projeto.
E dentro das faixas limites de operação normal.
Além disso, deve conhecer a função e operação de cada componente do sistema.
Assim pode entender a operação combinada entre os vários componentes do sistema.
O operador deve estar familiarizado então com os seguintes componentes e operação:
Compressor em sistemas de refrigeração
Cada compressor tem um tipo e modelo.
E ainda que seja do mesmo fabricante, possui uma série de limites operacionais.
Estes limites definem assim a faixa de aplicação.
Isto é, essa é a qual cada compressor pode operar de maneira segura.
Os limites mais importantes são protegidos por controles de segurança.
Os quais o operador deve estar familiarizado com os pontos de ajuste e função.
Agora vamos destacar então os principais elementos de controle:
- Baixa pressão de sucção;
- Alta pressão de descarga;
- Baixa pressão diferencial de óleo;
- Alta temperatura de descarga;
- Baixa temperatura de descarga;
- Alta temperatura de óleo;
- Altas correntes do motor elétrico;
- Outros controles de segurança específicos para cada tipo de compressor.
Válvulas de controle automático em sistemas de refrigeração
A função básica das válvulas de controle é regular de forma automática a pressão.
Além da temperatura, nível ou vazão de injeção de fluido refrigerante.
Nos vários componentes do sistema.
É importante saber então:
O funcionamento da válvula. Princípio de operação e condições.
As funções de regulagem da válvula e como ajustá-la.
Para determinada condição de operação e controle.
O que acontece com o sistema quando a válvula abre ou fecha?
Ou se a válvula for isolada do restante ou houver um “bypass” manual.
Algo que acontece com a válvula e o sistema em casos de falha de energia.
E se a válvula for então reenergizada.
Válvulas de bloqueio em sistemas de refrigeração
Explicamos sobre isso e muito mais em nossos Cursos Vaportec.
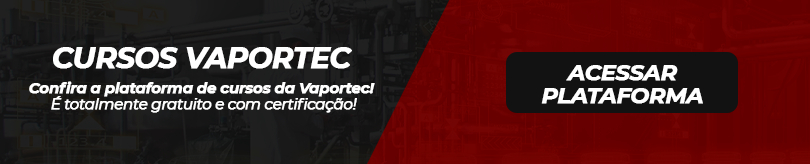
Estas válvulas são então instaladas no sistema.
Isto é, a função delas é isolar certos componentes do restante do sistema.
Ou ainda de bloquear/parar o fluxo de fluido refrigerante.
Elas podem então ser operadas de forma manual.
Ou através de comando elétrico, pneumático.
Até mesmo através de piloto pelo fluido refrigerante pressurizado.
É importante saber onde cada válvula de bloqueio está localizada no sistema.
Também o que acontece com o sistema quando se abre ou fecha a válvula.
Qual a posição normal de operação da válvula (aberta ou fechada).
E como determinar então se a válvula está aberta ou fechada.
Quando não há assim uma indicação externa evidente.
Válvulas de alívio de pressão: de segurança
As válvulas de alívio de pressão têm uma função essencial.
Evitar que haja rupturas devido à pressão excessiva em vasos de pressão.
Ou ainda compressores, trocadores de calor e descargas de bombas de amônia.
Além de em alguns trechos da tubulação.
Todas as válvulas de segurança precisam ser inspecionadas.
Isso deve ser feito então de forma periódica.
Conforme os requisitos da legislação.
O operador deve saber a localização das válvulas de alívio de pressão no sistema.
Assim como, o ponto de ajuste correto de cada válvula dessas.
Cada válvula deve ser identificada de forma distinta e “tagueada”.
• Qual componente ou parte do sistema cada válvula foi designada para proteger;
• Qual ação ou condição de desvio de operação deve ocorrer para que a válvula venha a atuar.
Controles elétricos/eletrônicos
O sistema de refrigeração possui vários componentes.
Alguns de controle elétrico ou eletrônico.
Tais como disjuntores, fusíveis, relés, temporizadores.
Além de malhas de controle.
Várias funções de proteção controladas por sistema computadorizados.
Isto é, muitos deles localizados em um painel elétrico.
No painel microprocessado ou ainda na tela de um sistema de supervisão.
E gerenciamento então do sistema de refrigeração.
É responsabilidade do operador conhecer então de forma plena:
- Componente ou parte do sistema designado para proteger;
- O que fazer em caso de falha de energia;
- O que acontece com o sistema em um período longo de desligamento;
- Qual a sequência de operação para desligamento completo do sistema;
- Qual a sequência de operação para a entrada em funcionamento do sistema;
- Como aliviar o sistema em elevação de pressão provocada por uma parada do sistema.
- Durante a uma falha de energia.
Mudanças de temperatura/pressão no sistema
São muitos os fatores que podem afetar então as temperaturas.
E pressões normais de operação do sistema de refrigeração.
Incluindo mal funcionamento mecânico ou elétrico.
Além de temperatura ambiente, carga de produto, etc.
É importante saber as condições de projeto e normais de operação do sistema.
Incluindo assim temperaturas e pressão de cada regime de operação.
Causas e efeitos em caso de mudança de temperatura ou pressão:
- O lado de baixa pressão do sistema;
- Na pressão intermediária para sistemas de duplo estágio;
- No lado de alta pressão do sistema.
Em caso de desvio operacional, que ações serão tomadas então.
Dessa forma pode restaurar as condições normais.
Da temperatura e pressão nos vários pontos do sistema.
Recolhimento de fluido refrigerante
Um sistema de refrigeração deve ser então bem projetado.
Assim deve incluir a facilidade de se transferir o fluido refrigerante.
De uma parte para outra do sistema com o propósito de manutenção.
Cada operador deve ser então bem treinado.
Para realizar assim operações de recolhimento.
Assim como de transferência em todas as partes do sistema.
Além disso deve saber que ação tomar.
Quando houver então uma elevação de pressão no sistema.
Quais as ações em caso de um vazamento não previsto.
E ainda como realizar as operações de recolhimento no sistema.
Ou manter vácuo nos diferentes componentes do sistema.
Para realização de reparos, além disso.
Manutenção preventiva em sistemas de refrigeração
Existem fatores importantes para a operação segura do sistema de refrigeração.
O maior deles, é o conhecimento do operador com relação à manutenção preventiva.
Incluindo então os vários componentes do sistema.
Cada componente requer assim uma rotina de inspeção.
Além disso, a limpeza ou ajuste interno. Para possível substituição então.
Algumas operações e revisões devem ser realizadas periódica.
Deve-se revisar os compressores conforme a periodicidade e requisitos do fabricante.
O óleo lubrificante deve-se inspecionar e substituir.
Conforme a periodicidade e requisitos do fabricante do compressor.
Os filtros, limpamos ou substituímos conforme recomendação do fabricante.
Caso seja necessário realizar manutenções com maior frequência.
Pode ser um indicativo de problemas relacionados à qualidade.
Ou à pureza da amônia no sistema.
Os controles de segurança se inspecionam e testam através de operação manual.
Para garantir que os mesmos estão funcionando de forma correta.
Quando em falha, deverão então ser substituídos de forma imediata.
Verificamos assim as válvulas de bloqueio quanto à vedação completa.
Através de manobras periódicas de inspeção de cada válvula.
O castelo deve estar livre de pintura ou ferrugem.
E o corpo da válvula livre de vazamento.
Válvulas de controle automático: em sistemas de refrigeração
Se verificam então através da sua operação manual.
Dessa forma, alguns componentes podem estar defeituosos.
Como as bobinas de solenóides e pilotos.
Além disso, pode haver nas partes internas e mecânicas.
Por isso substitua de imediato.
Filtros de linha antes das válvulas devem então ser limpos.
Em especial se for verificado alguma perda de capacidade.
Verificamos então os drenos de óleo.
O excesso de óleo remove-se então com a frequência necessária.
Há aumento da frequência de drenagem de óleo?
Esse é um sintoma que há arraste excessivo de óleo.
Isto é, dos compressores para o sistema.
Verificação das válvulas de expansão quanto ao ajuste correto.
Em caso de válvulas eletrônicas os sensores de pressão e temperaturas.
Deverão então ser calibrados de forma periódica.
Manômetros e Termômetros de Campo.
Bem como sensores temperatura e transdutores de pressão.
Programas de calibração periódica
Visores de Nível deve-se manter limpos e desobstruídos.
Devem ser protegidos então de maneira adequada.
Tubos de vidro devem ser evitados e substituídos.
Usando assim visores blindados com proteção externa.
Os controladores de nível e sensores de nível.
Além disso, alarmes de nível devem ser inspecionados.
E testados assim através de operação manual.
Para garantir então que os mesmos estão funcionando de forma correta.
Quando em falha, deverão ser substituídos de imediato.
Bombas de Refrigerante devem ser verificadas.
Quanto ao desempenho, por exemplo.
Através de medições constantes das pressões de sucção e descarga.
Além da corrente dos motores.
Deve-se revisar conforme a periodicidade e requisitos do fabricante.
Equipamentos de proteção individual e coletiva.
As máscaras, luvas, aparelhos autônomos de respiração.
Além de lava-olhos, chuveiros e sinalização de emergência.
Verifique então de forma regular.
Os procedimentos de emergência.
Devem ser executados de forma frequente.
Em exercícios simulados e revisados pelo menos a cada 2 anos.
Outros itens a serem inspecionados:
As tubulação de amônia e suportes da tubulação devem ser inspecionados quanto à vibração.
O isolamento térmico também deve ser verificado.
Em toda sua extensão quanto a danos.
Ou rompimento da barreira de vapor, condensação ou congelamento no revesti mento externo.
Vazamentos.
Uma boa instalação de amônia não deve ter vazamentos.
Caso sejam verificados traços de óleo em conexões flangeadas.
Ou próximo a válvulas se perceber o odor de amônia.
Os mesmos devem então ser verificados.
É importante uma verificação periódica nos vários pontos sujeitos a vazamentos na instalação.
Sistemas Hidrônicos devem então ser verificados.
Quanto à possibilidade de vazamentos.
Através de análise periódica da qualidade de água.
Se há traços de contaminação com Amônia.
Equipamentos de proteção individual
Todo operador trabalhando na sala de máquinas.
Deve usar um conjunto de equipamentos para proteção individual.
Que dependerá da atividade em questão então.
Adotam-se óculos, botas e capacete na maioria dos casos.
Nas operações onde há risco de vazamento de Amônia a proteção respiratória é essencial.
E deve incluir pelo menos uma máscara de proteção facial com filtro apropriado.
As situações de emergência podem gerar condições bem mais severas.
Do que aquelas observadas na operação do dia a dia.
Para essas situações, uma brigada de emergência deve assumir o controle da situação.
A qual deverá estar munida de equipamentos de proteção individual especiais.
Antes de iniciar assim qualquer ação corretiva.
Em sistemas de refrigeração por Amônia.
Recomenda-se os seguintes equipamentos de auxílio aos operadores.
E então à brigada de emergência:
Os capacetes, óculos, botas, capas e luvas de neoprene.
Todos eles para proteção corporal contra radiação, respingos, objetos em queda.
Para todos os operadores e membros da brigada de emergência.
Já as máscaras panorâmicas proporcionam proteção respiratória.
Deve-se dispor para atividades operacionais sujeitas a pequenos vazamento de amônia.
Onde a concentração de amônia for menor que 500 ppm.
Não deve ser usada em locais confinados.
Onde existam excesso de vapores ou nuvem tóxica.
Recomenda-se que cada operador possua sua máscara e seja treinado para utilizá-la.
Os filtros devem ser verificados e mantidos dentro do prazo de validade.
Equipamento de Respiração Autônoma (SCBA).
Proporciona proteção respiratória total numa operação de resgate.
De pessoas intoxicadas ou controle de situações críticas.
Ainda mais em locais confinados.
O cilindro deve ter autonomia mínima de 20 min.
Recomenda-se que hajam pelo menos dois equipamentos desses na instalação.
E que estejam localizados de forma estratégica.
Em abrigos apropriados e em posição de serem vestidos de forma rápida.
Roupas de Proteção de Nível “A”.
É o macacão de PVC ou Borracha Clorobutílica.
Com botas e luvas de neoprene ou borracha incorporadas ao macacão.
Que 18 proporcionam total proteção corporal.
Para os casos onde há necessidade de controlar vazamentos de Amônia líquida.
Ou quando for necessário entrar dentro da nuvem tóxica.
Recomenda-se que haja pelo menos um conjunto completo desses.
Na instalação junto com os equipamentos de respiração autônoma.
Os operadores da sala de máquinas devem ser treinados na sua utilização.
Pois em caso de grande vazamento.
Os mesmos deverão utilizá-las para acesso à sala de máquinas.
Para identificação da fonte de vazamento e procedimentos específicos.
Como o fechamento de válvulas para cessar o vazamento.
Equipamentos de proteção coletiva: sistemas de refrigeração
Nas operações de resgate de pessoas.
Quando atingidas por respingos ou jatos de amônia
Ou ainda intoxicadas pela inalação de vapores.
São necessários os seguintes equipamentos:
• Chuveiro de emergência e lava–olhos: deverão ser instalados próximos às portas de saída da sala de máquinas;
• Manta para fogo e maca. Cobertor, estojo de primeiros socorros e garrafa de oxigênio com máscara. A serem mantidos em abrigos apropriados e de fácil acesso à brigada de emergência.
Sistemas de refrigeração: conclusão
Você pode continuar seus estudos lendo nosso ebook sobre:
Segurança em sistemas de amônia.
Clique aqui para baixar.
Quer saber mais sobre conteúdos assim?
Temos diversos Cursos da Vaportec que podem ajudar você a crescer na sua carreira.
São profissionais experientes na área que montaram materiais de qualidade.
Clique aqui para se cadastrar nossa plataforma.
Estamos à disposição.
Um abraço